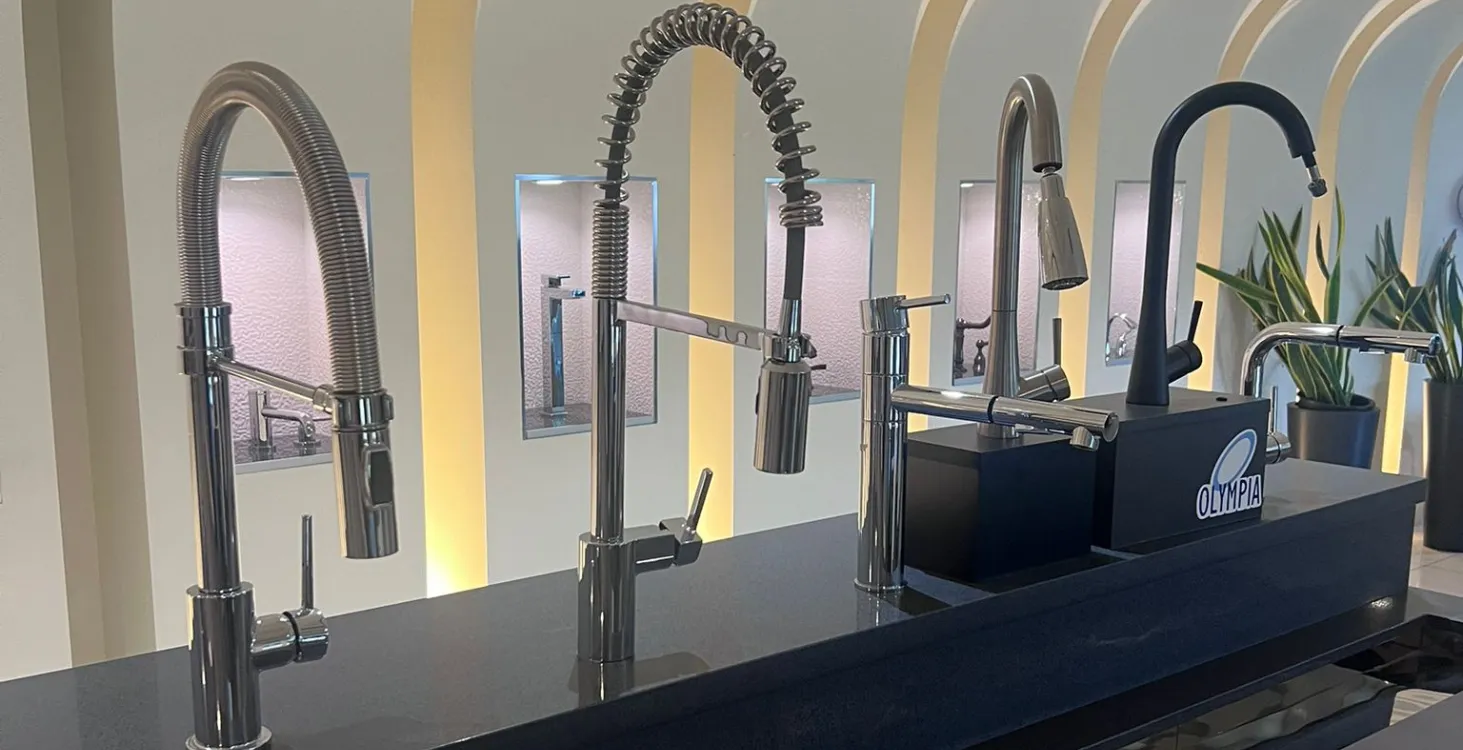
Behind the Scenes: How Pioneer Faucets are Made
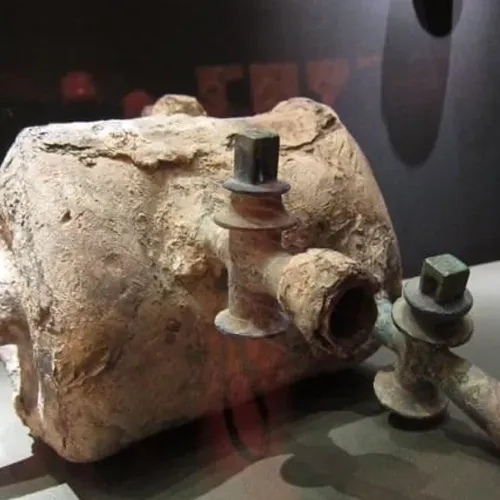
We know we’re (very) biased, but the faucet-manufacturing process is a fascinating one! The first faucets we know of were invented and used on Crete in approximately 1700 BCE. The ancient Romans had surprisingly modern faucets that worked much the same way ours do today. In modern times, the faucet design and creation process is a streamlined and efficient one. Faucets have never been so beautiful or worked so well. For all those who have wondered how we make our faucets, here’s a behind-the-scenes look!
Step 1: Selecting and Casting Metal
The first step of the process is selecting a high-quality metal and beginning the casting process. Here at Pioneer, we find that the most durable faucets tend to be made of brass due to its durability and corrosion resistance and stainless steel for its modern look and rust resistant design. After selecting the metal, we melt it and then pour it into one of our state-of-the-art die-cast molds. These molds are designed to form faucets for various applications, from a kitchen sink, to a bathtub faucet, to a laundry room faucet, and allowed to cool into shape. Once these faucet spouts have been completed, they move onto the next step.
Step 2: Connecting the Spout to the Base
Next, silver solder is applied to the inside tip of the spout, followed by the addition of a threaded tip. The base is then coated with flux paste and soldered into the hub at the base of the faucet. This prepares the faucets to later be fit with an aerator at the end of the spout, while the hub allows it to later be connected to the handles and basin of the sink.
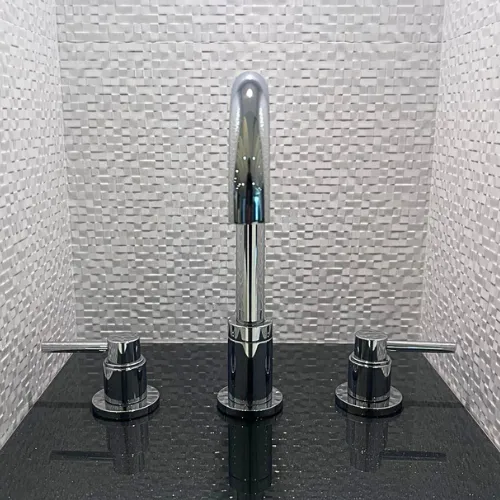
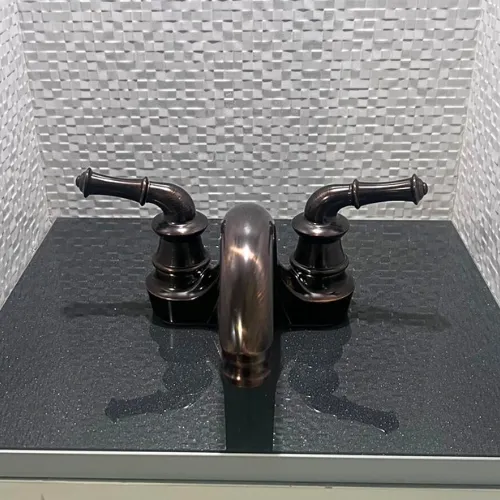
Step 3: Polishing Metal and Applying Finish
Our faucets then move on to our polishing wheels, which polish them to a mirrored surface. This prepares them to then be coated with any of our premium finishes, such as brushed nickel, chrome, oil rubbed bronze, matte black, or brushed gold. Each finish begins with a layer of corrosion-resistant nickel. To do this, the faucets and hubs are dropped into an acid bath laced with dissolved nickel, that is then electroplated onto the faucets by running an electric current through the bath. To add further plating such as chrome, the faucets are dumped into a further chromium plating bath and connected to a negatively charged cathode, causing the chromium ions to coat the faucet in a layer of chromium up to 1 micron thick. The same process can be swapped out for a bath of gold. For a matte black finish this process can be done by electroplating with a bath of black nickel and chromium, or through Physical Vapor Deposition (PVD), where the faucet is placed in a vacuum chamber and exposed to heated vaporized metal compounds. These vapors are then hit with an electric current, causing them to bond to the faucet on a molecular level, which creates an incredibly durable matte black finish.
Step 4: Cutting and Forming the Body of the Faucet
Meanwhile, the body of the faucet is formed with advanced machines cutting a rod of brass into a threaded cylinder. Waterways are then drilled to accommodate hot and cold inlets, handles, and valves. These holes are then connected with brass and copper tubes and then connected to the base plate. In Olympia’s washerless models, a hollow steel ball is drilled to create a ball valve that aligns with the water lines, allowing the handles to control temperature and flow.
Pioneer faucets use ceramic cartridges featuring smooth ceramic discs to control water volume and temperature with precision. Central Brass faucets use compression stems, which control flow by manually opening or closing a passage inside the faucet body.
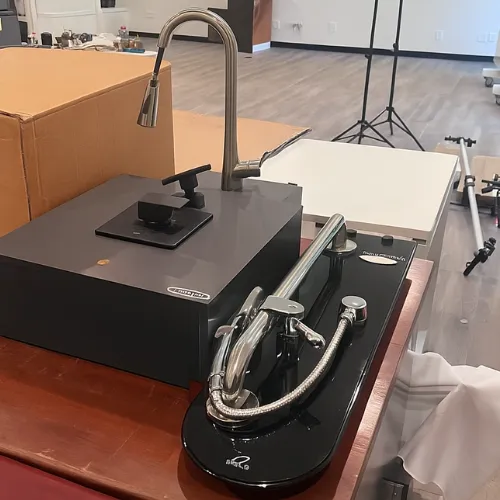
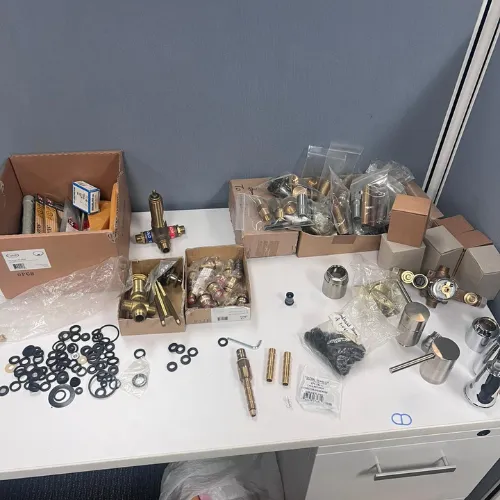
Step 5: Applying Seals, Aerators, and Ball Valves
Rubber seals are then inserted into the inlet holes, around the faucet valves, and inside of the ball valve to ensure a watertight seal. Rubber o-rings are then added to the body, forming another water tight seal and allowing the faucet handles to move. The ball valve is then inserted into the body of the faucet and capped off with a final rubber seal.The faucet spout is then fitted with an aerator at the tip of the spout before being attached to the body of the faucet with a metal bonnet, preparing the faucet for its final testing before the final touches are completed. Depending on the model, this may involve installing a ball valve (Olympia), a ceramic cartridge (Pioneer), or a compression stem (Central Brass).
This process primarily reflects Olympia’s washerless models. Central Brass faucets use compression stems with no cartridge, while Pioneer models use ceramic cartridges for smoother control and longer life. Manufacturing methods also vary—components may be cast or forged depending on the faucet line. At this point, the faucet is nearly ready for final testing and assembly.
Step 6: Quality Testing
Each faucet then undergoes rigorous quality testing using air, water, or other methods based on tests required to ensure watertight performance and proper connectivity to the water line. Depending on the model and test type, we use water, air, or other methods to check flow, function, and seal integrity, including detecting any pinhole leaks or connection issues. Technicians connect water to the faucet base and confirm that both the hot and cold sides flow properly while inspecting for any possible leakage points. Only faucets that pass every inspection move to final assembly.
Step 7: Final Assembly
In the final step, we attach the faucet to its matching handle or handles, completing the assembly. It is then thoroughly polished one last time before it is packaged and ready to be sent out to by plumbing and building specialists as well as DIY enthusiasts.
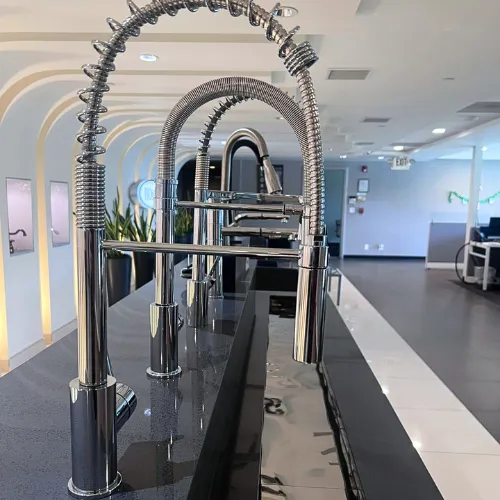
Wrapping Up
Through nearly forty years of hard work and dedication, Pioneer Industries has continued to refine and perfect this process to make the highest-quality faucets in the industry. We hope this behind-the-scenes look at the faucet-making process has helped you understand the craftsmanship and precision involved. We encourage you to continue your faucet research by exploring our wide range of premium faucets, fixtures and other products at Pioneer Industries.
Pioneer, Olympia, and Central Brass
As a trusted supplier of faucets and fixtures for over 100 years, Pioneer, Central Brass, and Olympia are here for you. All our faucets are backed by a best-in-the-industry warranty, are easy to install, and will stand the test of time.
We’ll Save You Money and Time
There are many ways to the same destination. This saying applies to multifamily housing builds just as much as to anything else in life. The ultimate goal is save as much money as possible while delivering a great finished project – that’s simply showing smart business sense. But, finding a one-off deal or sacrificing quality isn’t the only way to get a healthy ROI. We have a better way.
Pioneer works with professionals every day to develop specification packages and plans that save our valued partners both time and money, sometimes in surprising ways. It’s our goal to ensure your project meets or exceeds its expected outcome. We want to get to know you and your company and show you how we can save you money. Please reach out via our website form or call us at (800) 338-9468.
Some of Our Favorite Products: